Transferring an image onto fabric is a great way to personalize your clothing, accessories, or home decor. Whether you're creating a custom t-shirt or adding a unique design to a pillow, the process allows you to bring your creative ideas to life. It’s easy to get started, and with a few simple tools, you can make high-quality transfers right at home. In this guide, we’ll cover everything you need to know about transferring images onto fabric, from choosing the right materials to applying your design with precision.
Choosing the Right Fabric for Image Transfer
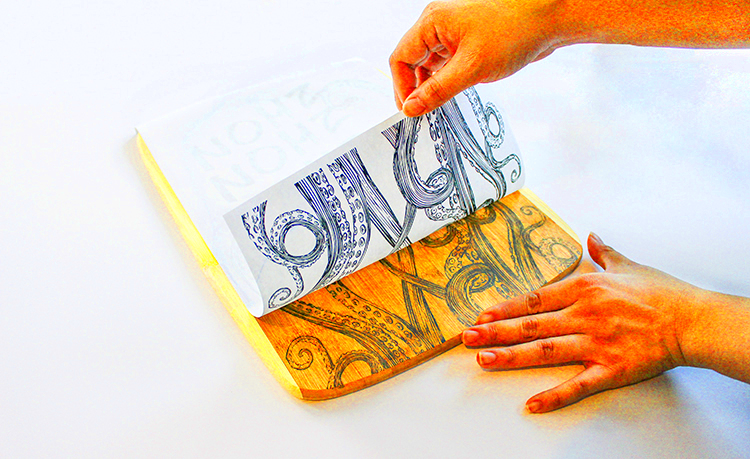
The first step in transferring an image onto fabric is choosing the right fabric. Not all fabrics are created equal when it comes to holding printed designs. Some materials work better than others, ensuring that your image transfer is smooth and long-lasting. Here are a few fabrics that are ideal for
- Cotton: This is the most popular fabric for image transfers. It absorbs ink well and creates vibrant, clear designs.
- Polyester: Ideal for heat transfer vinyl (HTV) methods, polyester fabrics work well with most transfer techniques, offering durability and vivid colors.
- Blends: Cotton-polyester blends are also good choices, as they combine the best qualities of both materials.
When choosing fabric, think about the design’s durability, the feel of the fabric, and the type of transfer method you plan to use. Fabrics like silk and stretchy materials are not always ideal for transfers as they can distort the image. For a professional finish, always test your fabric before starting a full project.
Also Read This: Quick Guide to Cropping Images in MS Paint
Preparing the Image for Transfer
Before you can transfer your image onto fabric, it needs to be prepared properly. Here are some important steps to follow:
- Choose the Right Image: Select a high-resolution image. Low-quality images may appear blurry when transferred.
- Edit the Image: If needed, adjust the image size and resolution. You can use photo editing software to resize the image to fit the area of your fabric.
- Reverse the Image (for Certain Methods): If you’re using transfer paper, make sure to flip the image horizontally. This ensures that it prints the correct way once transferred.
- Print the Image: Use the right kind of printer and transfer paper for your chosen method. Inkjet printers work best for most transfer papers, while laser printers are suitable for others.
Properly preparing your image is essential to ensure that your design looks great on the fabric. Spend time adjusting and editing the image to your liking before printing it. A little effort during the preparation stage can make a huge difference in the final result.
Also Read This: How to Refine an Image in MidJourney
Methods for Transferring the Image onto Fabric
There are several methods for transferring images onto fabric, each with its own advantages and ideal uses. Choosing the right method depends on the type of fabric, the complexity of the design, and the tools you have available. Here are some common methods you can use:
- Iron-On Transfer Paper: This is one of the easiest methods for beginners. You simply print your image onto special transfer paper and then iron it onto the fabric.
- Heat Transfer Vinyl (HTV): HTV involves cutting out your design from vinyl sheets and then using heat to bond the vinyl to the fabric. It’s perfect for bold, graphic designs.
- Screen Printing: This method is best for mass production of designs. It involves creating a stencil (or screen) and using ink to print the design onto fabric.
- Sublimation: Sublimation is ideal for polyester fabrics and involves turning ink into gas that bonds directly with the fabric. This method results in vibrant, long-lasting designs.
Each method has its pros and cons. For example, iron-on transfer paper is simple and effective for smaller projects, while screen printing is better for larger, bulk projects. It’s essential to choose the method that best suits your design and fabric type to achieve the best results.
Also Read This: Print on Demand and Shutterstock Images: Exploring Usage Rights and Licensing Opportunities
Using Iron-On Transfer Paper for Fabric
Iron-on transfer paper is one of the most popular methods for transferring images onto fabric because it’s affordable and easy to use. Here’s how to use it step by step:
- Print Your Image: Start by printing your image onto the transfer paper using an inkjet printer. Make sure you print in reverse (mirror image) if your design has text or complex details.
- Prepare the Fabric: Prewash the fabric to remove any coatings or sizing that could interfere with the transfer. Iron out any wrinkles for a smooth surface.
- Cut Out the Design: After printing, cut out your design, leaving a small border around it for easier placement on the fabric.
- Iron the Design: Place the printed side of the transfer paper facing down onto the fabric. Use a hot iron (without steam) to press the design onto the fabric. Follow the instructions on the transfer paper packaging for heat and time settings.
- Peel Off the Backing: Once the transfer paper has cooled, carefully peel off the backing to reveal the transferred design.
This method works best on cotton or polyester fabrics. However, keep in mind that the transfer may fade over time, especially if the fabric is washed frequently. To extend the life of the transfer, wash the fabric inside out in cold water and avoid using harsh chemicals.
Also Read This: How to Buy Adobe Stock: A Step-by-Step Guide
Printing and Applying the Design
Once you’ve chosen your transfer method and prepared your image, it’s time to print and apply it to the fabric. Whether you’re using iron-on transfer paper or another method, the application process is key to achieving a professional-looking result. Here’s how you can go about it:
- Check Printer Settings: Before printing your design, ensure your printer settings match the type of transfer paper you’re using. Some transfer papers require specific printer settings like “photo quality” or “high resolution” for the best print quality.
- Align the Design: When applying the design to the fabric, make sure it’s aligned properly. Use a ruler or fabric adhesive to help hold the design in place before applying heat.
- Apply Even Pressure: Whether using an iron or a heat press, apply even pressure across the entire design. This ensures that the image transfers evenly and that all edges of the design bond with the fabric.
- Allow the Design to Cool: After applying heat, let the fabric cool completely before removing any protective sheets or backing from the design. This prevents smudging and ensures the image sticks well to the fabric.
- Final Touches: Once the design is transferred, give it a final touch by carefully ironing it again, especially around the edges, to make sure everything is securely bonded.
Proper printing and application are crucial steps to ensure that the design is clear, vibrant, and durable. Remember to follow the instructions specific to your transfer method to avoid common mistakes like fading or peeling. With the right tools and techniques, you can create stunning custom fabric designs that will last for years.
Also Read This: How to Remove Getty Images from Your Photos
Caring for Fabric with Transferred Images
Taking care of fabric with transferred images is essential to ensure your design lasts for as long as possible. Proper care can help preserve the vibrancy and integrity of the design while preventing fading, peeling, or cracking. Here are some tips for maintaining your fabric with transferred images:
- Wash with Care: Always wash your fabric inside out to protect the design. This reduces friction and helps prevent the image from rubbing off. Use cold water and a gentle cycle to maintain the design's appearance.
- Avoid Harsh Chemicals: Avoid using bleach or strong detergents, as they can weaken the transferred image. Opt for mild, fabric-friendly detergents that are gentle on the print.
- Air Dry Instead of Using a Dryer: The heat from a dryer can cause the transferred image to crack or peel. It’s best to air dry your fabric after washing to keep the design in top condition.
- Iron Carefully: If you need to iron the fabric, do so on the reverse side or place a thin cloth over the design. Avoid direct contact with the iron on the image to prevent damage.
- Store Properly: When not in use, store items with transferred images in a cool, dry place away from direct sunlight. Prolonged exposure to sunlight can cause colors to fade.
By following these care tips, you can extend the life of your fabric with transferred images and keep your designs looking vibrant and fresh for years to come.
Also Read This: Converting RAW Images to JPG Format Easily
Common Mistakes to Avoid When Transferring Images
Transferring images onto fabric is a simple process, but there are a few common mistakes that can lead to less-than-ideal results. By being aware of these mistakes, you can avoid frustration and ensure a successful transfer. Here are some things to watch out for:
- Using the Wrong Fabric: Not all fabrics are suitable for image transfer. For example, fabrics with a lot of texture or stretch may distort the image. Always check the fabric type and compatibility with your chosen transfer method before starting.
- Incorrect Printer Settings: Printing an image with the wrong settings can lead to poor quality. Make sure your printer is set to the correct resolution and use the recommended type of paper for your transfer method.
- Not Prepping the Fabric: Failing to wash and iron the fabric before applying the transfer can result in poor adhesion. Pre-washing removes any coatings or chemicals that may interfere with the transfer process, while ironing ensures a smooth, even surface.
- Not Allowing Enough Drying Time: Whether you’re using transfer paper or HTV, it’s essential to let the fabric cool down after applying heat. Rushing the process may cause the design to shift or peel.
- Ignoring Manufacturer Instructions: Each transfer method has its own set of instructions for temperature, pressure, and application time. Ignoring these instructions can result in subpar results or damage to the fabric.
By avoiding these common mistakes, you can ensure a smoother transfer process and achieve the best possible results for your project.
Also Read This: Create Your YouTube Channel on an iPad and Begin Your Content Creation Journey
FAQ
1. Can I transfer any image onto fabric?
Most images can be transferred onto fabric, but the quality of the transfer depends on the fabric and the method you use. High-resolution images work best, especially when using transfer paper or HTV.
2. How long will the transferred design last?
The lifespan of a transferred design depends on the method and how well you care for the fabric. Iron-on transfers may fade over time, while HTV designs tend to last longer if properly maintained.
3. Can I wash fabric with transferred images?
Yes, you can wash fabric with transferred images. Just make sure to wash it inside out, use cold water, and avoid harsh detergents or bleach. Air drying is recommended to preserve the design.
4. What fabrics are best for image transfers?
Cotton, polyester, and cotton-polyester blends are the best fabrics for image transfers. These fabrics hold the design well and result in vibrant, lasting images.
5. Do I need a special printer for transferring images?
For most transfer methods, an inkjet printer is sufficient. Make sure to use the correct transfer paper for your printer type, and always follow the manufacturer’s guidelines.
Conclusion
Transferring an image onto fabric is a creative and rewarding way to personalize your items, whether it’s for clothing, home decor, or gifts. By understanding the different methods, choosing the right fabric, and following proper care instructions, you can achieve a high-quality, lasting design. Avoiding common mistakes, such as using the wrong materials or ignoring instructions, will ensure a smoother process and better results. With the right tools and techniques, you’ll be able to bring your ideas to life and enjoy your custom fabric creations for a long time. Happy crafting!