Pepsi is not just a refreshing drink; it’s a global phenomenon loved by millions. Ever wondered how your favorite bubbly beverage is made? From the sourcing of ingredients to the final canning process, the production of Pepsi is a fascinating journey that involves both science and artistry. In this post, we’ll dive into the various stages of Pepsi production, shedding light on the critical ingredients that come together to create that iconic taste we all know and love.
The Ingredients of Pepsi
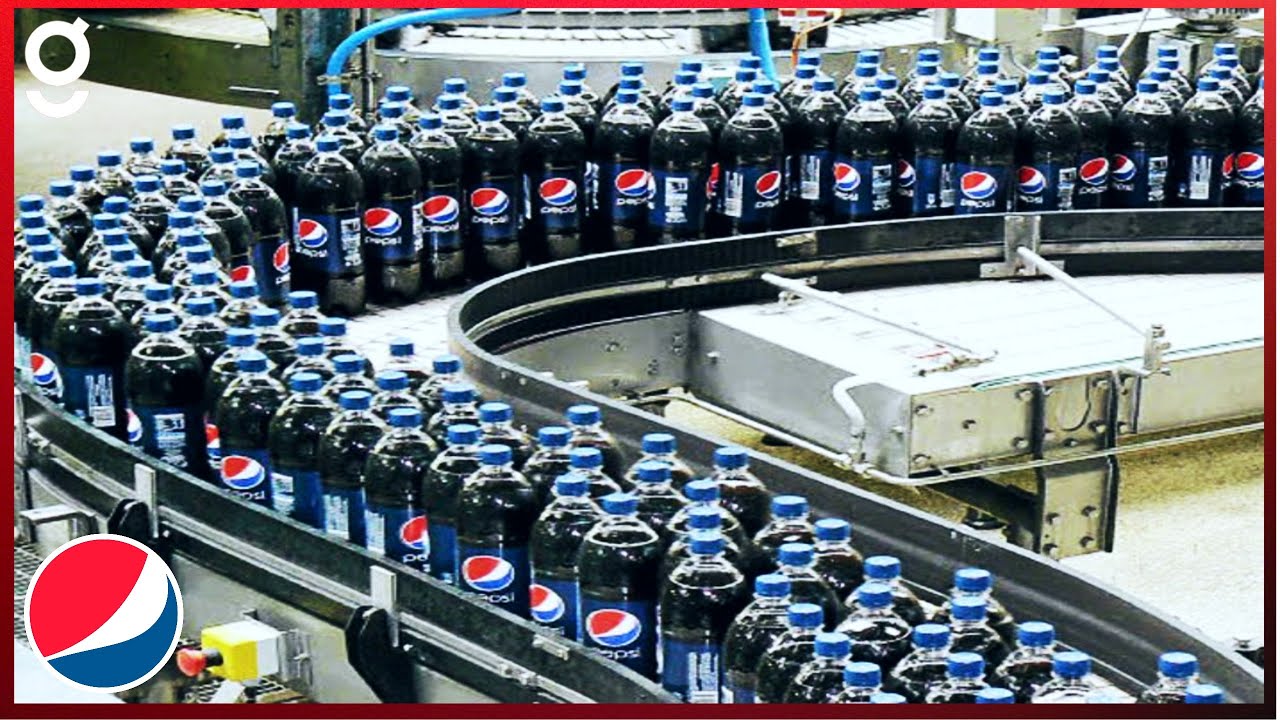
At the heart of any great beverage is its ingredients. For Pepsi, a harmonious blend of flavors and components works together to create that signature cola taste. Here’s a closer look at what goes into every can:
- Carbonated Water: The first and foremost component, carbonated water gives Pepsi its fizziness. Sourced from clean water supplies, it undergoes filtration and carbonation processes to reach just the right level of bubbly.
- High Fructose Corn Syrup (HFCS): This is the sweet stuff! HFCS provides the sweetness that Pepsi drinkers crave. It’s derived from corn starch and is often preferred in soft drinks for its cost-effectiveness and sweetness profile.
- Caramel Color: Ever wonder how Pepsi gets its distinctive brown color? It’s all thanks to caramel color, a food coloring created through the heating of sugars. This ingredient not only adds color but also a hint of flavor.
- Phosphoric Acid: This ingredient gives Pepsi its tangy kick. Phosphoric acid is a flavoring agent that enhances the overall taste experience and balances the sweetness.
- Caffeine: For many, the little boost from caffeine is a bonus in their beverage. Pepsi contains caffeine, which is a natural stimulant, adding to the drink's allure.
- Natural Flavors: A closely guarded secret! The unique blend of natural flavors in Pepsi—including flavors from citrus oils and spices—creates the signature taste that tantalizes the taste buds.
So, the next time you crack open a Pepsi, remember that it’s not just a simple soft drink. It’s a carefully crafted mix of ingredients topped off with a bit of magic from the production process!
The Manufacturing Process
The manufacturing process of Pepsi is a fascinating blend of technology and tradition. It’s not just about mixing ingredients; it’s about crafting a beverage that millions love. Let's break it down step by step:
- Ingredient Sourcing: The journey begins with sourcing high-quality ingredients. The key players are carbonated water, high fructose corn syrup (or sugar), caramel color, phosphoric acid, caffeine, citric acid, and natural flavors. Each ingredient undergoes strict selection to ensure they meet pre-defined quality standards.
- Water Filtration: Water is the backbone of any soft drink. Pepsi plants utilize advanced filtration systems to purify water, ensuring it is clean and free from impurities. This step is vital because any contaminants can affect the final product's taste.
- Mixing the Ingredients: After filtering, the water is mixed with sweeteners and flavorings. This is where the magic happens! The precise blend of ingredients is crucial and can vary slightly depending on regional preferences. The mixture is carefully monitored using sophisticated measuring devices.
- Carbonation: Next, carbon dioxide is added to the mix. This is what gives Pepsi its signature fizz. The carbonation process is closely controlled to achieve the perfect level of bubbles.
- Bottling & Packaging: Once mixed and carbonated, the beverage is bottled or canned. Modern bottling lines are highly automated, reducing the risk of contamination. The containers are sealed to lock in freshness and flavor.
- Distribution: Finally, the packaged Pepsi is loaded onto trucks and sent out to distributors, reaching grocery stores and restaurants near you.
Every step in the manufacturing process is designed to ensure consistency and quality in every sip!
Quality Control Measures
When it comes to soft drinks like Pepsi, ensuring quality is paramount. PepsiCo employs several quality control measures to guarantee that each bottle meets its high standards. Here’s an inside look at their quality control journey:
- Raw Material Inspection: Before any ingredients are used, they undergo rigorous testing. This includes checking for purity and verifying that they meet PepsiCo's specifications.
- In-Process Monitoring: Throughout the production line, samples are regularly taken and analyzed. This helps catch any deviations from the standard in real-time, ensuring the product remains consistent.
- Final Product Testing: After bottling, samples from each batch are tested for flavor, carbonation level, and visual appearance. This step is crucial because it ensures that only top-notch products leave the factory.
Quality Control Measure | Description |
---|---|
Ingredient Verification | Testing raw materials for purity and quality before production. |
Process Sampling | Regular sampling during production to monitor consistency and flavor. |
Final Batch Testing | Comprehensive testing of finished products to ensure they meet company standards. |
By implementing these comprehensive quality measures, PepsiCo takes its commitment to quality seriously, ensuring fans can enjoy a delicious, reliable beverage every time they pop a can.
5. Packaging and Distribution
Once the production process is complete and quality assurance checks have been passed, it's time for the exciting part—packaging and distribution! This stage is crucial as it determines how the product makes its way to the hands of thirsty consumers across the globe.
Pepsi is packaged in various formats to meet different consumer needs, including:
- Cans: Lightweight and recyclable, cans are a popular choice for convenience.
- Bottles: Available in several sizes, from small to family packs, bottles cater to diverse consumption occasions.
- Fountain Syrups: Used in restaurants and fast-food outlets, ensuring a fresh pour every time.
Each packaging type is designed not only for aesthetic appeal but also for preserving freshness and flavor. This is achieved through:
- Sealing: Airtight seals are employed to prevent any contamination.
- Labeling: Eye-catching labels provide essential information about the product, including nutritional facts and branding.
- Safety Testing: Packaging materials are rigorously tested for safety to ensure they are free from harmful chemicals.
After packaging, the products are loaded into distribution trucks. Pepsi employs a well-strategized distribution network, often using a just-in-time approach to ensure freshness. From large warehouses to retail outlets, the journey is meticulously planned. With the help of technology like GPS tracking, Pepsi can monitor deliveries, ensuring that the drinks reach their destination on time and in perfect condition.
6. Conclusion: The Journey of Pepsi from Factory to Consumer
The story of Pepsi is not just about a soft drink; it's a journey that starts from sourcing raw materials and ends with a refreshing can or bottle in your hand. Each step of the process, from sourcing ingredients to the intricate production methods, and finally to packaging and distribution, plays a vital role in maintaining the quality that Pepsi is known for.
Throughout this journey, several crucial elements come into play:
Stage | Key Element |
---|---|
1. Sourcing | High-quality ingredients |
2. Production | Advanced technology |
3. Quality Assurance | Rigorous testing |
4. Packaging | Aesthetic and functional design |
5. Distribution | Efficient logistics system |
Ultimately, the journey of Pepsi from the factory to the consumer is a well-orchestrated ballet of teamwork, technology, and tradition. So, the next time you crack open a cold Pepsi, take a moment to appreciate the meticulous work that made it all happen. Cheers!