Cement is the backbone of modern construction, playing a crucial role in the building of everything from roads and bridges to homes and skyscrapers. Understanding how cement is made and processed reminds us of its complexity and the significant role it plays in our daily lives. The cement production process involves various stages, from the extraction of raw materials to the final milling of the product. This blog post will walk you through this intriguing journey, shedding light on each method and material involved in transforming nature’s offerings into this essential building material.
Raw Materials Used in Cement Making
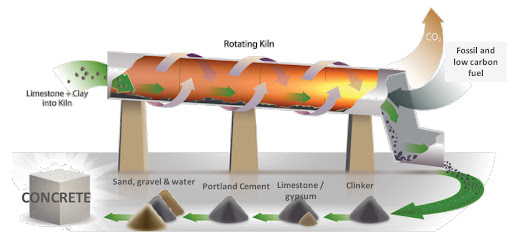
The production of cement begins with the careful selection of raw materials. These materials must contribute to both the chemical and physical properties of the cement, ensuring high quality and durability. Let’s take a closer look at the primary raw materials used in cement making:
- Limestone: This is the most significant ingredient in cement production, often comprising about 70-80% of the raw mix. Limestone provides calcium, which is crucial for the formation of clinker.
- Clay or Shale: These materials provide the necessary silica, alumina, and iron, contributing to the overall chemical composition of the cement. They usually make up around 20-25% of the mix.
- Gypsum: Gypsum is added during the final grinding process to control the setting time of the cement. This ingredient typically constitutes about 3-5% of the final product.
Other materials can include:
- *Fly Ash: A byproduct of coal combustion, which can enhance the durability of concrete.
- Slag: This material comes from the steel industry and can improve the properties of the cement.
- Natural Pozzolans: These occur in nature and can also enhance various characteristics of cement.
The careful combination and proportions of these raw materials yield the high-quality cement used throughout the construction industry. In the next sections, we will dive into the fascinating process of how these materials transform into the cement we rely on every day.
The Cement Manufacturing Process
The cement manufacturing process is an intricate journey that transforms raw materials into the quintessential binding agent essential for construction. While it may seem complex at first glance, breaking it down into digestible parts reveals a fascinating production pipeline.
To start with, the primary raw materials for cement production include limestone, clay, iron ore, and sometimes additional materials such as sand or ashes. These components are carefully selected for their chemical compositions, which influence the quality of the final product. The process begins with the crushing and grinding of these materials to create a fine powder called raw meal.
Next, the raw meal is heated in a rotary kiln at temperatures exceeding 1,400°C. This intense heat causes a series of chemical reactions that form clinker—small, hard nodules that are the backbone of cement. After heating, the clinker cools down, and additives like gypsum are mixed with it to regulate the setting time of the cement.
Finally, the cooled clinker is ground into a fine powder to produce cement, which is then packaged or transported to concrete manufacturers and construction sites.
To summarize, here are the key steps in the cement manufacturing process:
- Extraction of raw materials
- Crushing and grinding
- Heating in rotary kiln
- Cooling
- Grinding with additives
Steps Involved in Cement Production
Cement production involves a series of critical steps that ensures the raw materials are transformed into a high-quality product ready for construction. Let’s dive deeper into these steps to understand what each entails.
1. Extraction and Preparation of Raw Materials
The process begins as limestone and other materials are extracted from quarries. The rock is then crushed and mixed to achieve the proper chemical composition. This stage is crucial, as the quality of the raw materials directly impacts the final cement quality.
2. Blending and Homogenization
Next, the crushed materials undergo blending to ensure a uniform feed into the kiln. Homogenization techniques, including rotary drum mixing, help achieve a consistent chemical makeup, which is vital for producing high-quality cement.
3. Pre-calcination
In some modern facilities, pre-calcination is employed to partially refine the raw meal before it enters the kiln. This step significantly enhances efficiency and reduces energy consumption during the heating process.
4. Clinker Production
As mentioned before, the raw meal is heated in a rotary kiln, where it undergoes physical and chemical transformations to become clinker. This process results in the formation of critical compounds essential for the strength and durability of the cement.
5. Milling and Packaging*
The final step involves grinding the clinker along with gypsum and other additives to achieve the desired fineness. The finished product is then packaged or consigned to bulk transport, ready for distribution.
By understanding each step involved in cement production, we can appreciate the precision and intricacy required to create this indispensable building material, helping our world to be built one structure at a time.
Quality Control Measures in Cement Manufacturing
Quality control is paramount in the cement manufacturing process, ensuring that the final product meets stringent standards for performance and durability. Here are several key quality control measures that manufacturers commonly implement:
- Raw Material Testing: Before the production begins, raw materials such as limestone, clay, and additives undergo rigorous testing. Professionals check for chemical composition, moisture content, and other parameters to ensure optimal quality.
- Process Monitoring: Throughout the cement manufacturing process, from crushing to clinker formation, various indicators are monitored. This includes temperature control in the kiln, where the correct heat levels are vital for proper chemical reactions.
- Laboratory Testing: The quality of cement is checked through laboratory testing, including compressive strength tests, fineness tests, and soundness tests. These ensure the cement meets regulatory standards and customer specifications.
- Continuous Quality Feedback: Many modern plants utilize advanced technologies such as real-time monitoring systems. These systems provide continuous feedback during the process, allowing for immediate adjustments to maintain quality.
By maintaining an unwavering commitment to quality, cement manufacturers can produce a reliable product that not only meets customer expectations but also performs well in construction applications, reinforcing the overall safety and durability of structures.
Environmental Impact of Cement Production
Cement production is recognized as one of the most carbon-intensive industries globally. It contributes significantly to greenhouse gas (GHG) emissions due to the energy-intensive nature of the process and the chemical reactions involved. Let’s explore some key aspects of its environmental impact:
Impact Area | Description |
---|---|
Greenhouse Gas Emissions | Cement production accounts for approximately 8% of global CO2 emissions. This comes from both fossil fuel combustion and the chemical transformation of limestone (CaCO3) to lime (CaO). |
Resource Depletion | High-quality limestone and clay are essential for cement; their extraction can lead to habitat destruction and biodiversity loss. |
Energy Consumption | The process requires vast amounts of energy, primarily sourced from non-renewable fossil fuels, contributing further to environmental degradation. |
Water Usage | Cement plants require significant water for various processes; this can strain local water resources, especially in arid regions. |
To mitigate these impacts, many companies are investing in more sustainable practices, such as using alternative fuels, implementing carbon capture technologies, and exploring new materials that might lessen reliance on traditional cement. As awareness of climate change grows, the industry must adapt to balance production with environmental stewardship.
How Cement is Made and Processed
Cement is a fundamental material in construction, serving as the primary binding agent in concrete and mortar. The production of cement involves several key processes that transform raw materials into the finished product. Below, we explore the main stages of cement manufacturing and the materials involved.
1. Raw Materials
The primary raw materials for cement production include:
- Limestone (Calcium Carbonate)
- Clay (Silicates, Alumina)
- Gypsum (used to regulate setting time)
- Other additives (such as iron ore and fly ash)
2. The Manufacturing Process
The cement manufacturing process can be broken down into the following stages:
Stage | Description |
---|---|
Extraction | Natural raw materials are extracted from quarries. |
Crushing | Extracted materials are crushed and ground into a fine powder. |
Raw Meal Preparation | The raw materials are blended to achieve the desired composition. |
Clinker Production | The raw meal is heated in a kiln to form clinker, a nodular material. |
Cement Grinding | Clinker is ground with gypsum to produce cement. |
Through this process, cement is produced in various types, including Ordinary Portland Cement (OPC), Rapid Hardening Cement, and Sulfate Resisting Cement, each designed for specific applications in construction.
Conclusion and Future of Cement Production
The future of cement production lies in sustainability and innovation. With a growing emphasis on reducing carbon emissions, the industry is exploring alternative materials, energy-efficient technologies, and innovative methods such as carbon capture. As these advancements continue to evolve, the cement industry will play a vital role in building a greener future.