Transferring images to shirts is a fun and creative way to personalize your clothing. Whether you want to design a unique gift or create a shirt that reflects your personal style, this process is relatively simple. You don’t need to be a professional designer to get started. All you need is the right image, some basic tools, and a little patience. In this guide, we will walk you through the essential steps of transferring images to shirts so you can get the best results every time.
Choosing the Right Image for Transfer
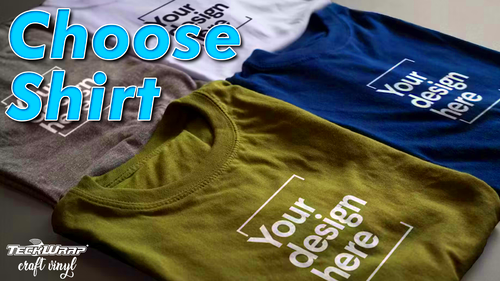
The first step in creating a custom shirt is choosing the right image. Not all images are suitable for printing on fabric, so it’s important to pick one that will transfer well and look great. Here are some key factors to consider:
- Resolution: High-resolution images (300 dpi or higher) ensure that your design appears crisp and clear on the shirt.
- Colors: Consider how the colors will look when printed on fabric. Bright, bold colors tend to pop, while very light or dark colors might not transfer as well.
- Complexity: Keep in mind that very complex images may not look as good when transferred to fabric. Simple designs with clean lines usually give the best results.
- Format: Opt for images in formats like PNG, JPEG, or TIFF. PNG is especially good because it allows for transparent backgrounds, which works well with shirt printing.
Take the time to select an image that fits your shirt design idea and meets these criteria for the best outcome.
Also Read This: How to Save a High-Resolution Image from Google Slides or PowerPoint
Preparing the Image for Shirt Printing
Once you’ve selected the perfect image, the next step is to prepare it for printing. This involves several key steps to ensure the design looks great when transferred to the shirt:
- Resize the Image: Make sure your image is the right size for the shirt. You can adjust the image dimensions using an image editor. A good rule of thumb is to keep it between 8 and 12 inches wide, depending on the shirt size.
- Crop the Image: If there’s unnecessary space around the design, crop it to focus only on the part you want to print. Most image editing software allows you to easily crop your image.
- Invert the Image: If you’re using transfer paper, you may need to flip the image horizontally, especially if it has text or intricate details. This ensures it will appear correctly when transferred.
- Enhance the Image: Make any color adjustments or touch up the design to ensure that it will look its best on the fabric. Brightening the colors and increasing the contrast can help make the design stand out.
Once your image is ready, you’re all set to print it onto transfer paper. Taking these preparation steps will help ensure that the transfer looks sharp and professional on your shirt.
Also Read This: How to Read Metadata of an Image
What You Need for Image Transfer
Before you begin transferring an image to a shirt, it’s important to gather all the necessary materials. Having the right tools makes the process smoother and ensures a professional-looking result. Here’s a list of what you’ll need:
- Image Editing Software: Software like Adobe Photoshop, GIMP, or even online editors can help you prepare and resize the image for printing.
- Transfer Paper: Special transfer paper is designed for printing your image, which you’ll later transfer onto the shirt. Make sure to choose the right type of transfer paper for the fabric you’re using (light or dark fabrics require different papers).
- Printer: A good-quality inkjet printer is usually best for printing images onto transfer paper. Ensure your printer is compatible with the transfer paper you are using.
- Heat Press or Iron: You can use a heat press for better, more even results, but an iron can work if you don’t have one. Just make sure it gets hot enough to properly press the image onto the fabric.
- Shirt: Choose a fabric that is suitable for image transfer. Cotton works best, but you can use other fabrics as long as they can withstand heat.
- Scissors: You’ll need scissors to cut the transfer paper and trim your image before applying it to the shirt.
- Wax Paper or Parchment Paper: This can be used to protect the transfer during the pressing process, preventing the image from smudging or the heat press from damaging the fabric.
With these materials in hand, you're ready to move forward with the image transfer process!
Also Read This: Follow This Easy Guide for Beginners on How to Use Streamable
How to Use Transfer Paper for Shirt Printing
Transfer paper is essential for transferring your image onto a shirt. Here’s how to use it correctly:
- Choose the Right Transfer Paper: There are different types of transfer paper for light and dark-colored fabrics. Make sure to buy the right one for your shirt color. For light fabrics, use transfer paper designed for light backgrounds, and for dark fabrics, opt for paper designed for dark backgrounds.
- Print Your Image: Load the transfer paper into your printer. Be sure to print the image on the correct side of the transfer paper—most papers will have a designated side that’s meant for printing. Remember, if your image includes text, you’ll need to flip it horizontally before printing.
- Let the Ink Dry: After printing, allow the image to dry for a few minutes to avoid smudging when transferring it to the shirt.
- Cut the Image: Use scissors to cut around the image, leaving a small border around the design. Be careful when cutting around the image, especially if it has intricate edges, as this can affect the final result.
- Preheat Your Shirt: Before transferring the image, preheat the area of the shirt where you’ll apply the image. This helps the transfer paper stick better and ensures an even application.
- Transfer the Image: Place the transfer paper onto the shirt with the printed side down. Follow the manufacturer’s instructions for the temperature and duration of pressing. If you’re using an iron, apply firm pressure and move it slowly over the transfer for even coverage.
- Remove the Transfer Paper: Once the image has cooled down, carefully peel off the transfer paper. You should be left with a vibrant, permanent print on the shirt.
With these steps, you’ll get a sharp, vibrant image that looks great on your shirt!
Also Read This: How to download Shutterstock images without watermark for free
Steps for Transferring an Image to a Shirt
Now that you’ve gathered your materials and prepared your image, it’s time to transfer it onto the shirt. Follow these steps for a smooth and successful transfer:
- Step 1: Prepare the Image – Use your image editing software to resize, crop, and adjust the colors of your image. Ensure it's the correct size for your shirt and save it in the proper format (e.g., PNG or JPEG).
- Step 2: Print the Image – Load your transfer paper into your printer. Print the image in high quality and make sure the printer settings match the paper type you're using (usually for photo paper).
- Step 3: Cut the Image – Once the image is printed and dry, use scissors to cut around the design. Leave a small margin around the edges, especially if there is text or fine details in the image.
- Step 4: Prepare the Shirt – Lay your shirt flat on a clean surface. Make sure it's wrinkle-free by ironing it lightly, as wrinkles can distort the transfer.
- Step 5: Heat Press or Iron the Transfer – Preheat your iron or heat press to the recommended temperature for the transfer paper you’re using. Place the transfer paper on the shirt with the printed side facing down. Apply heat and pressure for the recommended time, typically around 30-60 seconds.
- Step 6: Remove the Transfer Paper – Once the transfer is complete, allow the shirt to cool for a moment. Carefully peel off the transfer paper, starting from one corner, to reveal the design on the shirt.
- Step 7: Set the Design – If necessary, use an iron to gently press the design for a few seconds to set it further, ensuring the design is smooth and fully adhered to the fabric.
Once you’ve completed these steps, your custom shirt is ready to wear or gift. The result will be a vibrant, durable print that looks fantastic and can last through multiple washes if cared for properly!
Also Read This: Getting Your Pictures from Adobe Stock Subscription
Common Mistakes to Avoid During the Transfer Process
When transferring an image to a shirt, it’s easy to make a few mistakes, especially if you’re new to the process. By being aware of common errors, you can avoid frustrating results and achieve a professional-looking design. Here are some common mistakes to watch out for:
- Incorrect Image Orientation: One of the most common mistakes is printing the image in the wrong orientation. If your image has text or directional elements, remember to flip it horizontally before printing. Failure to do so can result in a backward image when transferred.
- Using the Wrong Transfer Paper: Different fabrics require different types of transfer paper. If you’re using a light-colored shirt, make sure you choose transfer paper designed for light fabrics. Similarly, for dark fabrics, use transfer paper meant for dark shirts.
- Not Preheating the Shirt: Preheating the shirt ensures the fabric is smooth and helps the transfer paper stick better. Skipping this step can lead to uneven transfers or a poor bond between the image and fabric.
- Too Much Pressure or Heat: Applying too much heat or pressure can damage the fabric or cause the image to warp. Follow the recommended temperature and time for the transfer paper you are using to avoid this issue.
- Not Letting the Ink Dry: After printing the image, it’s important to let the ink dry before proceeding. Smudging or smearing can happen if you rush through the process and handle the print too soon.
- Peeling the Paper Too Early: Don’t peel the transfer paper off the shirt immediately after pressing. Let it cool slightly, as removing it too early can cause the image to smudge or not fully adhere to the fabric.
By avoiding these mistakes, you can ensure a smoother and more successful image transfer process that results in a high-quality, durable custom shirt.
Also Read This: Discover the Age of Alaska Violet on YouTube and Insights Into Her Content
Tips for Long-lasting Custom Shirts
Custom shirts can be a fun and personal way to express yourself, but if you want your design to last, it’s essential to care for it properly. Here are some tips to help extend the life of your custom-printed shirts:
- Wash Inside Out: Washing your shirt inside out helps protect the printed design from rubbing against other clothes, which can cause fading or peeling. This small change can significantly increase the lifespan of your design.
- Use Cold Water: Wash custom shirts in cold water to prevent the fabric and design from shrinking or fading. Hot water can break down the transfer material over time, leading to cracks or discoloration in the design.
- Avoid Harsh Detergents: Choose mild detergents when washing custom shirts. Harsh chemicals can weaken the transfer, causing it to fade or peel faster. Stay away from bleach and other strong cleaning agents.
- Air Dry Instead of Using a Dryer: Air drying your shirt helps preserve both the fabric and the printed design. The heat from a dryer can cause the image to deteriorate or crack over time. If you must use a dryer, select a low heat setting.
- Iron Carefully: If you need to iron your custom shirt, do so on a low heat setting and avoid ironing directly over the design. Place a cloth or parchment paper over the print to protect it from heat damage.
- Store Properly: When not in use, store your custom shirts in a cool, dry place away from direct sunlight. Prolonged exposure to sunlight can cause the design to fade and weaken.
By following these tips, you can help ensure that your custom shirt stays vibrant and in great condition for a long time. Proper care is key to keeping your design looking fresh!
Also Read This: Why Can’t I Create a YouTube Channel
FAQ
Here are answers to some of the most common questions people have when transferring images to shirts:
- Can I use a regular inkjet printer for shirt transfers?
Yes, you can use an inkjet printer as long as it’s compatible with the transfer paper you’re using. Just make sure to use high-quality paper for the best results. - How long will a custom shirt design last?
With proper care, a custom shirt design can last for years. Following washing and drying tips will help preserve the design. - Can I use any type of fabric for transfers?
While cotton is the best fabric for transfers, you can also use polyester and blends. However, the process might vary slightly depending on the fabric type. - Do I need a heat press to transfer the image?
A heat press is ideal for the best results, but you can also use an iron. Just make sure to apply the correct amount of heat and pressure, and follow the instructions for your transfer paper. - How do I prevent the transfer from cracking or peeling?
Ensure the image is properly applied with the right temperature and pressure. Additionally, take good care of the shirt by washing it inside out in cold water and air drying it. - Can I transfer an image to a dark shirt?
Yes, but you’ll need to use transfer paper designed specifically for dark fabrics. This type of paper has a white background that allows the colors of the image to stand out.
If you still have more questions or need help with the process, don’t hesitate to reach out. We’re here to help make your custom shirt creation experience as smooth as possible!
Conclusion
Transferring images to shirts is a creative and enjoyable process that allows you to make custom designs for gifts, personal use, or special occasions. By following the right steps, avoiding common mistakes, and using quality materials, you can achieve vibrant, lasting designs. Whether you’re printing a simple logo or a complex graphic, attention to detail will ensure a successful result. Remember to care for your custom shirts properly by washing and drying them with care to keep the design looking fresh for years. With the right tools and a bit of practice, you’ll be able to create professional-quality shirts at home!