Designing images for sublimation printing is a creative and technical process that requires careful planning. Whether you’re creating designs for t-shirts, mugs, or other products, it's important to understand how sublimation works and how to create high-quality images that will look great once printed. This guide will help you navigate through the essentials of sublimation image design, ensuring your final product meets your expectations. With the right tools and knowledge, you can create stunning, vibrant designs that stand out.
Understanding Sublimation Printing and Its Requirements
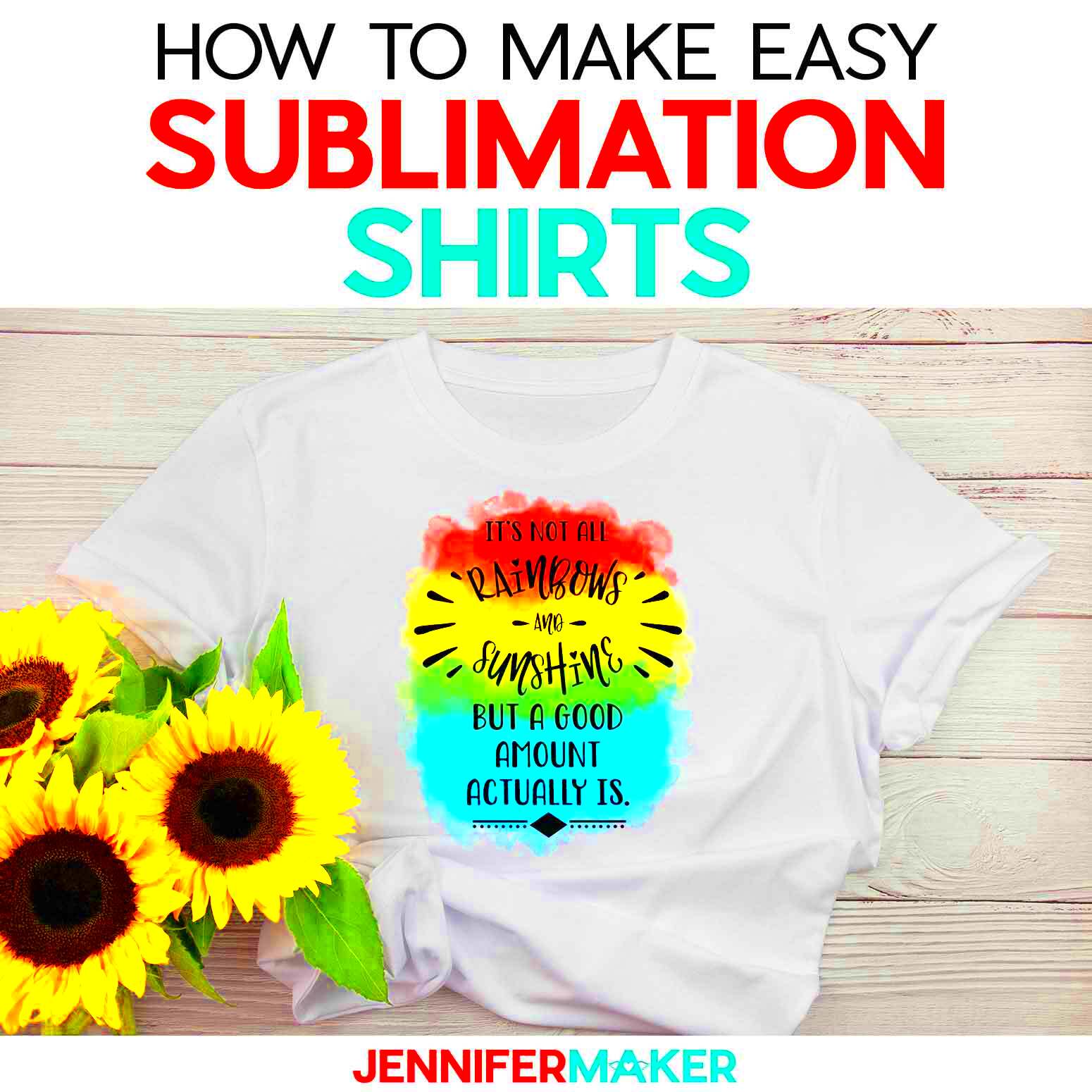
Sublimation printing is a unique process that uses heat to transfer dye onto materials such as fabric, metal, or ceramic. The dye is converted into a gas and bonds with the fibers or surface of the material, creating a permanent, vibrant image. Understanding the basics of sublimation printing is key to designing effective images that will turn out well.
- Materials: Sublimation printing works best with polyester fabrics or polymer-coated items like mugs and phone cases.
- Printer and Ink: A specialized sublimation printer and sublimation inks are required to achieve the best results.
- Heat Press: A heat press machine is essential to transfer the design from paper to the product surface using heat and pressure.
Keep in mind that sublimation works by heating the ink to turn it into a gas that bonds with the material. This means your designs must be high-quality, color-accurate, and suitable for the materials you're using. The proper setup is crucial to achieving the best results.
Also Read This: How to Create a 3D Image from a 2D Image: A Step-by-Step Guide
Choosing the Right Software for Designing Sublimation Images
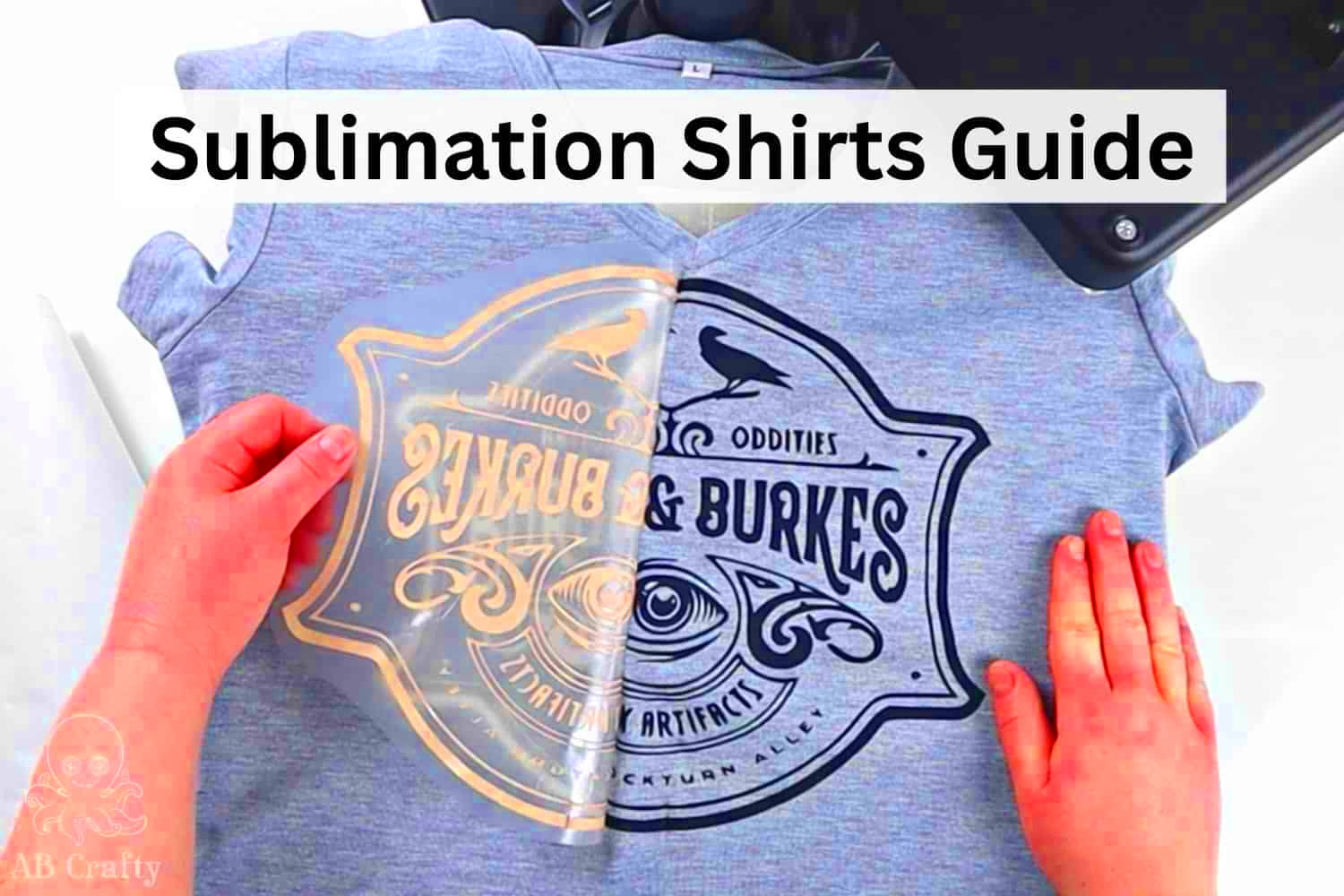
The software you use to create your sublimation images plays a significant role in the quality of your final product. Here are some of the best options for designing images specifically for sublimation printing:
- Adobe Photoshop: A professional-grade tool that allows for detailed image manipulation, ideal for creating complex designs.
- CorelDRAW: Popular among graphic designers, CorelDRAW is known for its vector editing capabilities, which are great for sublimation designs.
- Inkscape: A free, open-source vector graphics software that’s perfect for beginners and hobbyists.
- Affinity Designer: A more affordable alternative to Adobe Illustrator with powerful features for both vector and raster designs.
When choosing your software, consider the type of design you’re creating. For detailed, photo-realistic images, raster-based software like Photoshop is ideal. If you're working with logos or text-based designs, vector software like CorelDRAW or Inkscape may be more suitable. Regardless of your choice, make sure the software allows you to work with high-resolution files to ensure sharp, clear prints.
Also Read This: How to Sell Photos on Getty Images and Maximize Your Earnings
Preparing Your Image for Sublimation Printing
Preparing your image for sublimation printing is an important step to ensure your designs look great on the final product. It’s not just about creating a stunning image but also about making sure it translates well to the material you're printing on. Here’s what you need to do:
- Check Image Size: Your image needs to be the correct size for the item you're printing on. Measure the area where the design will appear, and adjust your image dimensions accordingly.
- Invert Your Image: If your design includes text or any other elements that need to appear in a specific orientation, you must flip the image horizontally before printing. This ensures it will look correct when transferred to the product.
- Remove Backgrounds: If you have a design with a background that doesn’t need to be printed, use your software to remove it. This gives the design a clean look when transferred to your item.
- Check for Bleed: Make sure your design extends beyond the edges of the printable area, so it covers the entire surface once printed. This is especially important for edge-to-edge prints on products like mugs or shirts.
Once these steps are done, you’re ready to print! Always double-check your work before moving forward to ensure everything is properly aligned and ready for sublimation.
Also Read This: How to Round Corners of Images in Google Slides
Best Practices for Color Management in Sublimation Designs
Color management is crucial in sublimation printing, as it ensures your design's colors come out as expected on your final product. Since sublimation uses heat to transfer the ink onto the material, it's essential to maintain color accuracy throughout the design process.
- Use CMYK Color Mode: Sublimation printers work best with the CMYK (Cyan, Magenta, Yellow, Black) color model. Always design in this color mode to ensure accurate color reproduction during printing.
- Calibrate Your Monitor: Colors can look different on your screen than they do in print, so regularly calibrate your monitor to match real-world colors. This helps you create designs that look just as vibrant when printed.
- Test Colors on Fabric: Always print a test image on the material you plan to use. Colors can appear different depending on the fabric or coating, so testing is essential for getting the best results.
- Use ICC Profiles: ICC profiles are a great way to ensure that the colors on your screen match those that will appear on your product. Many sublimation printers and software offer ICC profiles that help with color accuracy.
By following these best practices, you can avoid color mismatches and ensure that your designs look vibrant and true to your original vision when printed.
Also Read This: Using Adobe Stock Templates in InDesign for Your Projects
Optimizing Image Resolution and Quality for Sublimation
For the best results in sublimation printing, your image resolution and quality must be optimized. High-resolution images ensure sharp, clear prints that look professional and vibrant on any product. Here are a few tips to get the best results:
- Use High-Resolution Images: Aim for a resolution of at least 300 DPI (dots per inch) when preparing your image for sublimation. This ensures crisp, clear prints, especially for detailed designs and text.
- Avoid Scaling Up: Avoid enlarging low-resolution images. When you increase the size of a low-res image, it becomes pixelated and loses quality. Start with the highest resolution image possible.
- Choose the Right File Format: Save your image in a high-quality file format, such as PNG or TIFF. These formats preserve the image’s quality and support transparency, which is useful for designs without backgrounds.
- Keep the Aspect Ratio: Always maintain the correct aspect ratio of your image when resizing. Distorting your image can lead to poor print quality, especially on large items like posters or shirts.
By ensuring your images have the right resolution and are properly formatted, you’ll be able to achieve the best results with sublimation printing, making your designs stand out with sharp details and vibrant colors.
Also Read This: Troubleshooting Video Upload Issues on YouTube
Common Mistakes to Avoid in Sublimation Image Design
Designing for sublimation printing requires careful attention to detail. Even small mistakes can result in poor print quality, dull colors, or even ruined products. Here are some common mistakes to avoid when designing sublimation images:
- Low-Resolution Images: Using low-resolution images can result in blurry or pixelated prints. Always aim for at least 300 DPI to ensure your designs come out sharp and clear, especially for detailed work.
- Incorrect Color Mode: Designing in RGB (Red, Green, Blue) color mode can lead to color mismatches when printing. Always work in CMYK (Cyan, Magenta, Yellow, Black) color mode for accurate color reproduction in sublimation.
- Ignoring Bleed and Safe Zones: If your design doesn’t extend beyond the edges of the printable area, you risk having unprinted edges or borders. Always include bleed in your designs to ensure they fill the entire space.
- Not Flipping the Design: Forgetting to flip the image horizontally before printing can lead to mirrored text or images. Always check this before printing, especially for designs with text or logos.
- Choosing the Wrong File Format: Using file formats like JPEG can lead to compression and loss of quality. Opt for high-quality formats such as PNG or TIFF for the best results.
Avoiding these mistakes can save time, resources, and frustration, ensuring your sublimation designs come out just as you envision.
Also Read This: Simple Steps to Mirror an Image on Epson Printers
Conclusion and Key Takeaways
Designing images for sublimation printing requires a balance of creativity and technical knowledge. By following the best practices outlined in this guide, you can create vibrant, high-quality designs that transfer beautifully to your products. Here are the key takeaways:
- Prepare your image properly: Ensure it’s the right size, resolution, and orientation for sublimation printing.
- Manage colors effectively: Use the CMYK color mode, calibrate your monitor, and test colors to achieve accurate results.
- Optimize your image resolution: Aim for at least 300 DPI for sharp, detailed prints.
- Avoid common mistakes: Check your design for errors like low resolution, incorrect color modes, and flipped images before printing.
With the right approach and tools, sublimation printing can produce stunning designs that are both professional and long-lasting. Take the time to prepare and optimize your images, and you’ll be on your way to successful sublimation projects.
Frequently Asked Questions
1. What is sublimation printing?
Sublimation printing is a process that uses heat to transfer dye onto materials like polyester fabric or polymer-coated items. The ink turns into gas and bonds with the material, resulting in a vibrant and permanent image.
2. What file format is best for sublimation printing?
For the best quality, use high-resolution file formats like PNG or TIFF. These formats preserve image quality and support transparency, making them ideal for sublimation designs.
3. Can I use any material for sublimation printing?
Sublimation works best with polyester fabric or items that have a polymer coating, like mugs, phone cases, and plaques. It doesn’t work on natural fabrics like cotton unless they have a special coating.
4. Why do I need to flip my image before printing?
Flipping your image horizontally ensures that it prints in the correct orientation, especially for text and designs that need to be seen in a specific way.
5. How do I avoid color issues in sublimation printing?
To avoid color problems, use the CMYK color mode, calibrate your monitor, and print test images to check how colors appear on your chosen material. Always use ICC profiles for accurate color reproduction.